Batteries pour les mobilités
- Zoom sur
- Batterie
Comment concilier usage, durabilité et autonomie des batteries pour les mobilités ?
Introduction
Dans un contexte d’émergence des Zones à Faibles Emissions (ZFE) et dans un objectif de verdissement de leurs activités, les particuliers et les entreprises doivent se tourner de plus en plus vers des motorisations électrifiées.
Manque d’autonomie, manque de polyvalence, durabilité des batteries, recharge lente : l’électrification est souvent perçue comme un ensemble de contraintes. La stratégie qui doit accompagner l’électrification a pour conséquence de devoir répondre à de nombreuses questions qui ne se posaient pas à « l’ère du pétrole » mais permettant aux entreprises de se réinventer via par exemple des schémas logistiques innovants et plus efficaces.
Après 4 Think Tanks dédiés à l’hydrogène, CARA a proposé le 4 mai dernier d’aborder un pilier des mobilités de demain, la batterie, via la question de la conciliation entre la durabilité l’autonomie et l’usage de ces dernières dans les mobilités.
Quatre points de vue sur le sujet ont été partagés et discutés : la vision de l’ADEME, le panorama des chimies de batteries par l’IFPEN, l’importance du refroidissement des batteries par Wattalps et enfin un retour d’expérience de la collaboration Neotrucks/ABB/FIRALP.
ADEME : Usages des batteries dans la mobilité, entre une solution de transition et un risque de transfert d’impacts
La batterie dans les mobilités
La France a mis en place un plan d’action visant à neutraliser les émissions de Gaz à Effet de Serre (GES) nationales. Ce plan d’action, la Stratégie Nationale Bas Carbone, repose sur 5 piliers répartis entre sobriété et technologie. L’objectif est de réduire de 28 % d’ici 2030 les émissions liées au transport et de 100 % d’ici 2050 par rapport à 2015.
On observe sur le schéma ci-dessus que le véhicule électrique est un levier incontournable via l’efficacité de sa chaine de traction et de la source d’énergie, qui est bas carbone dans le cas du réseau électrique français.
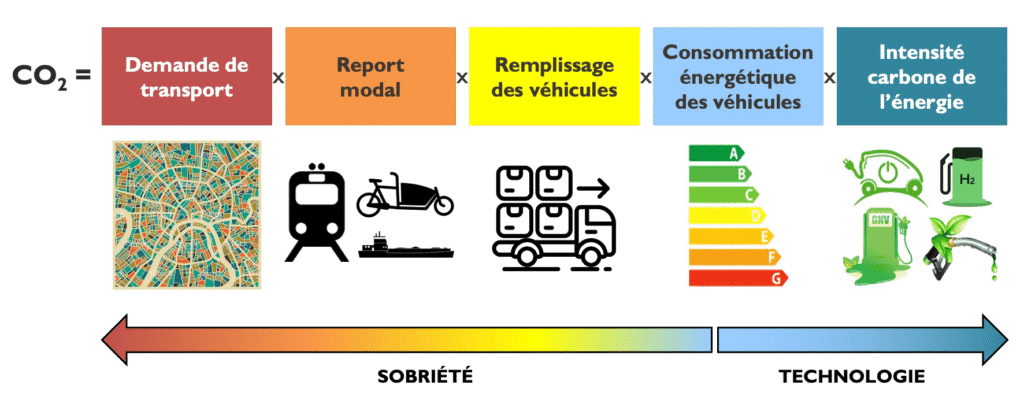
Dans ce schéma, l’ADEME subdivise la partie sobriété en trois 3 actions :
Maitriser: comprendre et agir sur la demande et les comportements, qui sont influencés par plusieurs variables, PIB, prix du pétrole, taux de motorisation. La modification des comportements peuvent aussi être subis, choisis ou induits par les modes de vie.Reporter: choisir les modes les moins impactant. Le transport routier est largement majoritaire alors que la majorité des déplacements sont courts et les alternatives deviennent performantes.Améliorer: améliorer l’existant pour limiter son impact. Les ambitions pour l’électrification sont fortes mais l’écart se creuse entre ces ambitions et la réalité. Il faut rendre le véhicule électrique (VE ci-après) accessible au plus grand nombre.
Rendre le véhicule électrique accessible au plus grand nombre signifie augmenter la production de batterie. Elle est l’élément critique de la chaine de traction électrique et représente entre 30% et 40% du coût du véhicule électrique. 50 gigafactories de 35 GWh/an seront nécessaires d’ici 2030.
En 2020 l’industrie considérait qu’une « bonne batterie en 2025-2030 » aura pour caractéristiques :
- 50$/kWh la cellule Li-ion capable de recharge rapide
- plus de 10 000 cycles
- plus de 2 millions de kilomètres
- 30 ans de durée de vie
- fabriquée avec des matières premières abondantes et recyclées
Néanmoins, à côté de ces exigences, de nombreuses questions se posent pour les industriels :
- Est-ce faisable ?
- Comment rendre agiles les gigafactories et les lignes de productions face à la diversité des chimies ?
- Quelle chimie pour quel usage ?
Les avantages de la mobilité 100 % batterie
Grâce au rendement élevé de la chaine de traction et de la possibilité de récupérer l’énergie cinétique lors des phases de décélération, les architectures tout-électriques sont considérées comme les plus sobres énergétiquement. Le véhicule électrique a donc aussi pour avantage d’avoir un faible impact sur le réseau électrique. Une baisse de la consommation électrique est même attendue d’ici 2040. Cela grâce à l’amélioration de la densité énergétique massique des batteries et de la densité de puissance massique des moteurs.
Remarque : une inadéquation entre production et besoin de recharge est néanmoins anticipée si le parc s’électrifiait (trop) rapidement.
Autre avantage, le Cout Total de Possession (Total Cost Ownership, TCO). Grâce à « l’Etude Energétique, Economique et Environnementale du Transport routier à horizon 2040 » (E4T 2040) menée par IFPEN pour l’ADEME, nous estimons qu’en 2040 le Véhicule Electrique (VE) restera plus cher à l’achat que son homologue thermique. Néanmoins son efficacité liée à une énergie moins chère permettra d’atteindre un TCO plus faible que celui d’un véhicule thermique utilisé aujourd’hui. Les tendances sont similaires pour les différents types de véhicules électriques. On note toutefois qu’un système comprenant à la fois des batteries et une pile à combustible à hydrogène apparait intéressant dans le cas des véhicules gros consommateurs d’énergie.

Batteries : Enjeux technologiques et sociétaux
Un des inconvénients de la batterie est sa consommation élevée en matière première. En effet, une batterie NMC de 75 kWh nécessite 210 kg de métaux (2,8 kg/kWh).
Ces métaux sont produits de manière inégale à l’échelle du globe. Par exemple 70 % du Cobalt vient de République Démocratique du Congo, 40 % du Nickel provient d’Indonésie, et l’Australie fournit environ 50% du Lithium (IEA 2021, The Role of Critical Minerals in Clean Energy Transitions).
L’enjeu pour l’Europe est d’importer la production de batterie pour passer de 87 % des GWh importés en 2020 à 67 % en 2030. Certains constructeurs font le choix d’internaliser la fabrication des cellules afin de diminuer les prix et sécuriser l’approvisionnement. Tesla souhaite même internaliser l’extraction du Lithium.
Autre enjeu pour la mobilité électrique : la non-adéquation des véhicules à batterie (BEV) aux « habitudes actuelles ». Un usager actuel roule avec son Battery Electric Vehicle (BEV) pendant 1h05 à 120 km/h et fait 25 mn de pause pour recharger alors qu’un usager de véhicule thermique roule 2h à 130 km/h avec 20 mn de pause. Solutions possibles :
- Augmenter la taille des batteries
- Limiter la vitesse des véhicules
- Diminuer la consommation
Remarque : il s’agit ci-dessus du message transmis par l’ADEME. Selon nous il faudrait faire accepter, lorsque c’est possible, la modification des usages pour être en mesure d’avoir des batteries plus petites et donc des véhicules plus légers, qui auraient pour effet de faire diminuer la consommation et de faire des recharges rapides plus fréquentes. Sur le sujet de la recharge des progrès ont été fait les batteries de 200-300 km supportent 4000-5000 cycles et permettent donc de parcourir un million de kilomètres.
Trois scénarii ont été identifiés par l’ADEME pour le développement des batteries :
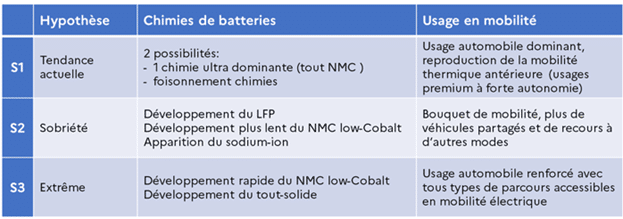
L’ADEME recommande de limiter la course aux performances en faisant appel à l’échange de batterie, la recharge dynamique, l’extendeur d’autonomie et l’intermodalité. La course aux performances dans un système fermé (la Terre) dont les réserve de Lithium sont fixes, risque d’empêcher l’accès au BEV au plus grand nombre et la réduction des GES, comme le montre la figure ci-dessous :
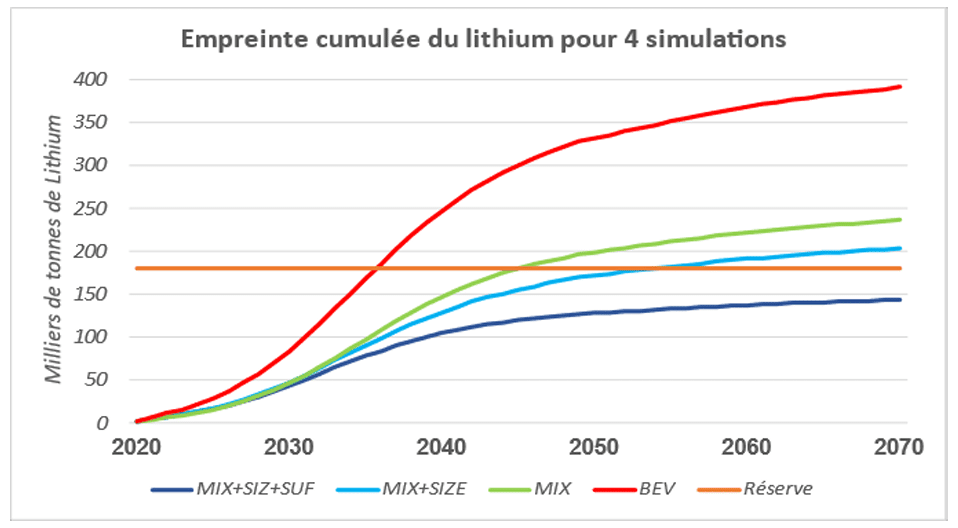
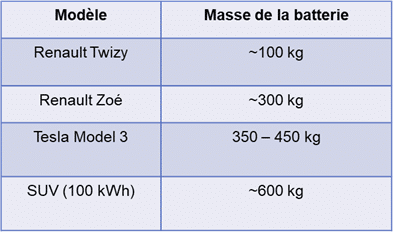
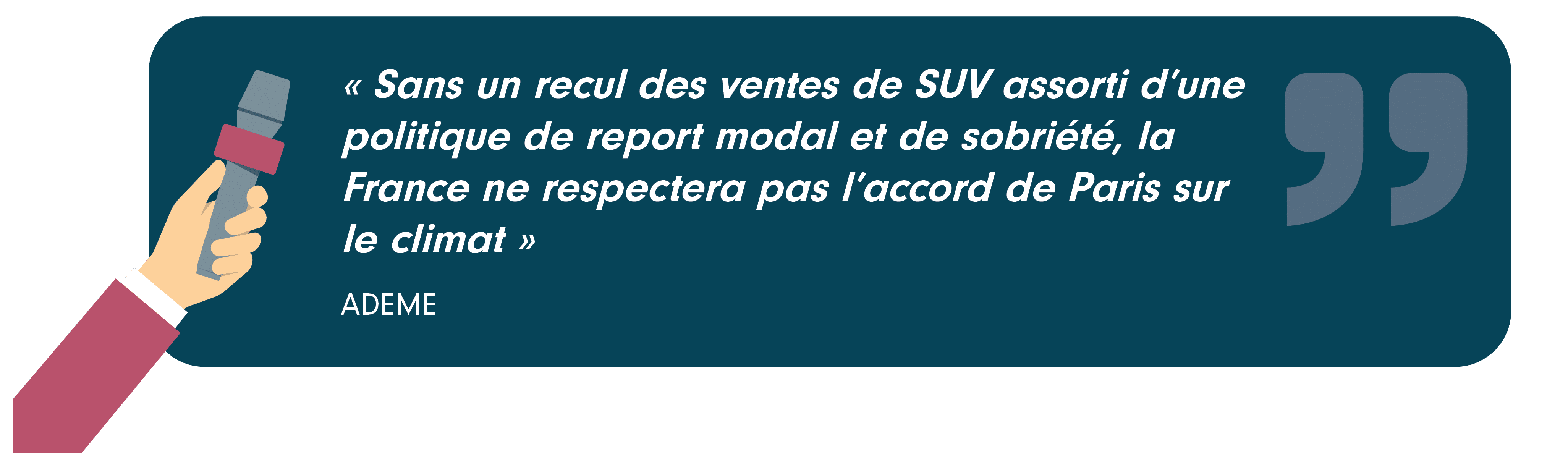
IFPEN : Batteries de traction, état de l’art et perspectives
La batterie est une « boite fermée »
Contrairement aux systèmes de stockage chimique de l’énergie, qui consistent à convertir de l’énergie chimique en chaleur, les systèmes électrochimiques convertissent de l’énergie chimique en énergie électrique. Parmi ces systèmes figurent les piles à combustibles, les batteries « conventionnelles », et les batteries à flux de matière telles que les métal-air.
Les batteries conventionnelles ont une particularité, l’énergie chimique est contenue dans le volume de la batterie sous la forme d’un couple Oxydant/Réducteur à chacune des électrodes. Ce couple est la matière active.
Les batteries conventionnelles sont des boites fermées ce qui implique que leur capacité de stockage dépend de la capacité des matières actives à stocker de l’énergie (contrairement à un moteur thermique pour lequel il suffit de doubler le volume du réservoir adjacent pour doubler l’autonomie).
Un réservoir d’essence de 50 kg génère 141 kWh utiles (25 % de rendement sur la chaine de traction) alors qu’une batterie de 50 kg génère 6,8 kWh utiles (rendement 85 %). Un facteur vingt sépare les deux malgré les progrès réalisés depuis 30 ans.
140 kWh sont-ils un objectif envisageable pour une batterie de 50 kg ?
En plus de cet objectif les batteries doivent faire face à de nombreux enjeux : sécurité, réparabilité, stockage performant, rapidité de la recharge, impact environnemental, durée de vie (10-15 ans).
Deux leviers principaux sont identifiés pour y répondre :
- La conception de la cellule
- La conception du pack
L’importance du packaging
En réalité, une batterie est le résultat de l’accumulation de nombreux composants qui chacun à son tour fait perdre de la densité massique/volumique d’énergie. Par exemple la cellule peut atteindre 245 Wh/kg mais l’intégration dans des modules eux-mêmes imbriqués dans des packs fait chuter la densité à 150 Wh/kg. Soit une réduction de près de la moitié. Des progrès sont possibles en optimisant le packaging des cellules.
A titre d’exemple, la batterie de la Renault Zoé est passée entre 22 à 41 kWh de 2012 et 2016 à volume constant. 80 % de l’augmentation de densité provient du design (optimisation du volume, collecteurs et séparateurs plus fins, électrodes denses et moins poreuses, …)
Au niveau chimique, avec la technologie Li-ion la meilleure densité obtenue commercialement est de 300 Wh/kg. Le tableau ci-dessous rappelle la classification européenne en matière de technologies.
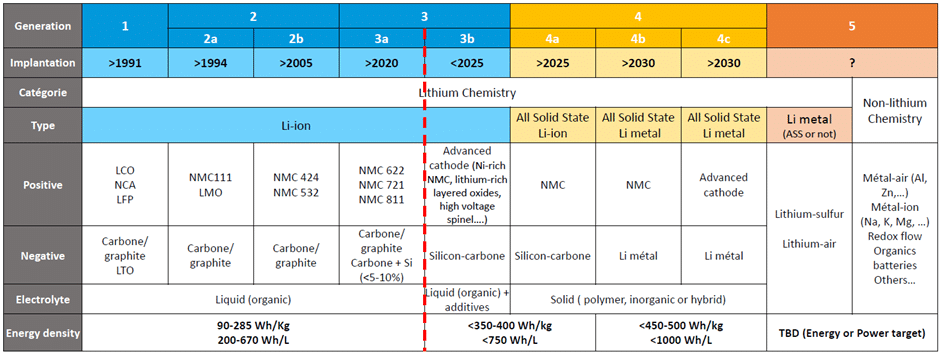
Des gains sont possibles mais une rupture technologique est nécessaire pour dépasser 400 Wh/kg. Elle est attendue d’ici 2025 avec l’apparition de la génération 3b de Li-ion.
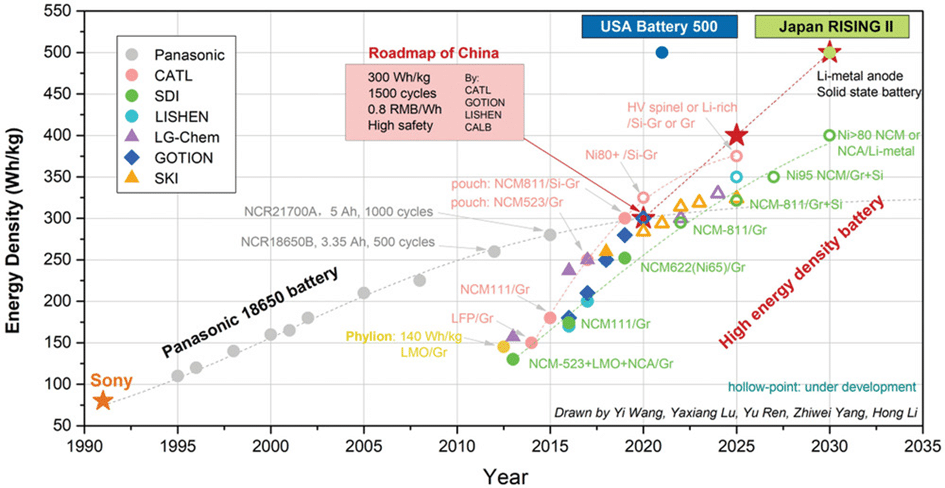
Source : Advanced Battery Materials ‐ Volume12, Issue17
Cependant, la course à la densité d’énergie engendre un problème de sécurité dans la mesure où cette course implique d’enrichir les batteries en Nickel. Or plus il y a de Nickel plus les batteries sont réactives et peuvent provoquer un emballement thermique. Autre conséquence de cette course, la densification des électrodes qui génère plus de chaleur et du « Lithium Plating » (qui peut mener aux dendrites). Dans ces conditions, un management thermique est obligatoire pour la sécurité et la durabilité du pack.
Le refroidissement thermique
La solution la plus déployée aujourd’hui est le refroidissement liquide indirect. Cela consiste à faire circuler un liquide, de l’eau glycolée, dans un circuit en contact avec les cellules. La solution est globalement efficace mais crée des hétérogénéités entre et intra cellules qui engendrent un vieillissement.
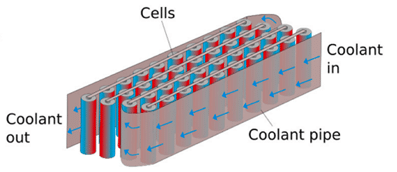
Technologie de refroidissement thermique indirect. Source : Immersion cooling for lithium-ion batteries Journal of Power Sources Volume 525, 30 March 2022, 231094
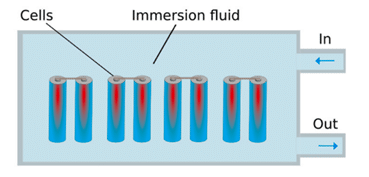
Technologie de refroidissement thermique direct. Source : Immersion cooling for lithium-ion batteries Journal of Power Sources Volume 525, 30 March 2022, 231094
Une solution alternative est en fort développement : le refroidissement direct par immersion. Comme son nom l’indique les cellules ainsi que les éléments internes chauffants (busbars) sont directement en contact avec le fluide. Ce refroidissement a pour avantages d’être très efficace et d’apporter une bonne homogénéité inter et intra cellule. La sécurité est aussi améliorée car l’immersion limite fortement le risque d’emballement thermique et sa propagation.
En revanche, l’immersion dans un fluide implique que le fluide en question doit répondre à un grand nombre de contraintes : isolation électrique, capacité et conductivité thermique élevées, ininflammabilité, légèreté, viscosité faible, bon marché, durabilité et absence de toxicité.
Le Cell to Pack (CTP)
Toutes les solutions présentées ci-dessus sont performantes mais chères. De leur côté, certains constructeurs chinois font le choix d’utiliser une technologie différente : le LFP/C au lieu du NMC. Ils font le choix d’utiliser une technologie qui offre une densité énergétique plus faible au niveau de la cellule mais optimisent au maximum l’intégration en pack. La technologie LFP fait son retour.
Deux gammes de batteries apparaissent alors sur le marché :
- Une gamme « Performance » riche en nickel
- Une gamme « bas prix/sécurité » à base de LFP
Des solutions existent pour compenser la perte de densité du LFP par rapport NMC :
- Supprimer le composant « module » => Cell to Pack
- Fabriquer des cellules de très grande taille pour leur intégration en pack => ratio matière active/packaging (Blade Battery par BYD = 202 Ah, 0,9 m, 4 kg, ratio matière active = 60 %, 150 Wh/kg)
Solutions applicables aux cellules NMC :
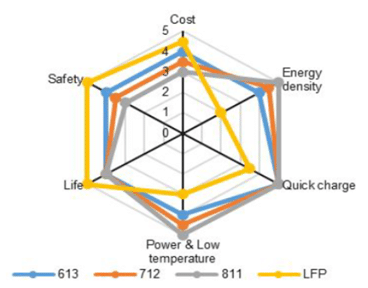
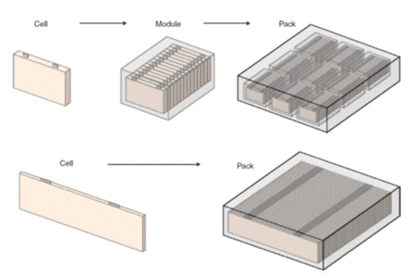
Remarque : La perte de densité du LFP peut être compensée principalement grâce à l’amélioration de la sécurité et par conséquent la réduction des exigences liées au casing.
Au-delà du CTP
Certains constructeurs de véhicules voient déjà au-delà du CTP avec par exemple le « Structural Battery Pack » (Tesla) ou le CTB « Cell to Body » (constructeur chinois). Dans ce cas les cellules sont directement intégrées au châssis du véhicule et assurent sa tenue mécanique. L’inconvénient est que les packs sont alors difficilement voire impossibles à démonter et donc à réparer ou recycler.
Les technologies « tout solide » et Na-ion, en cours de développement, apporteront aussi de nouvelles améliorations.
Wattalps : des batteries haute performance pour des engins industriels rentables
Alors qu’une voiture électrique est utilisée 1 à 2 heures par jour, les machines et engins industriels sont utilisés 3 à 8 h/j. Une machine vendue par un constructeur doit être rentable donc être :
- Productive : puissance constante, autonomie, capacité de charge rapide, pas de maintenance
- Durable : 10 000 => 15 000 heures d’opération et productivité en fin de vie
- Utilisable en toutes conditions : température (de -20 °C à +45 °C), poussière, sel, pluie
La plage d’utilisation ci-dessus est demandée alors que la température affecte fortement les performances de la batterie en matière d’autonomie. Par exemple, pour empêcher l’emballement thermique, la charge doit se faire au-dessous de 45 °C et la décharge en dessous de 60 °C.
Il faut que le vieillissement du pack soit homogène car la cellule la plus faible affecte tout l’ensemble. Le refroidissement joue donc un rôle central dans le ralentissement du vieillissement. Le refroidissement direct permet cela tout en apportant des fonctions supplémentaires : pré-conditionnement de la batterie, utilisation de l’inertie thermique du pack (batterie + fluide), utilisation de la climatisation habitacle et enfin utilisation du circuit hydraulique.
La solution choisie par Wattalps pour adapter la batterie à l’usage est d’avoir une approche modulaire. Les modules sont démontables et les pack Wattalps enregistrent aussi les données d’usage pour anticiper la seconde vie.